Paredes Moldadas In-Loco
No inicio do século passado, Thomas Edison já idealizava um processo de construção mais racional, utilizando paredes pré-moldadas, fundidas no próprio canteiro de obras na posição horizontal, para depois serem erguidas para a posição definitiva na vertical.Em 1910, uma igreja foi a primeira construção a ser erguida nos Estados Unidos seguindo essa ideia. A partir da década de 40, este processo passou a ser o preferido dos norte-americanos, por reduzir significativamente os custos e prazos de conclusão da obra.
Aqui no Brasil, a construção industrializada de paredes e lajes de concreto moldados in loco só começou a ser estudada e desenvolvida a partir da década de 90.Atualmente, as principais empresas que oferecem esse sistema são a Bilden, Inpar e Sergus.
Com algumas variações na sistemática de produção, o processo tem como base o conceito de construção industrializada, tendência mundial que vem ocupando cada vez mais espaço na cadeia de construtiva brasileira. O objetivo é oferecer custos reduzidos sem prejuízo da qualidade, segurança na construção, diminuição da necessidade de mão-de-obra, eliminação das patologias da alvenaria e redução nos prazos de entrega de obras.
PAREDES PERMITEM QUALQUER PROJETO DE ARQUITETURA
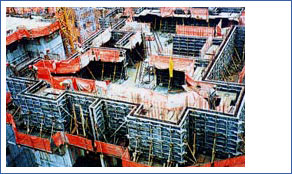
A Bilden Tecnologia em Processos Construtivos é uma das empresas que se especializaram em construções baseadas no sistema de paredes autoportantes pré-moldadas no próprio canteiro de obras.Segundo Sérgio Coelho, presidente da Bilden, “a pré-moldagem in loco é comprovadamente mais econômica do que a alvenaria convencional, os pré-fabricados ou a estrutura metálica”.
O sistema utilizado pela Bilden consiste, basicamente, na utilização de paredes com painéis arquitetônicos, autoportantes, pré-moldados em concreto armado, em grandes dimensões (40 a 70 m²), fundidos no próprio canteiro na posição horizontal, sobre piso de alta planicidade, previamente executado e nivelado a laser.Após atingirem a resistência necessária, os painéis são erguidos para a posição definitiva, na vertical, com o auxilio de guindastes apropriados.
Uma das vantagens desse sistema é que permite a realização de projetos de qualquer tamanho, com ofrmas regulares ou irregulares, e ampla variedade de tratamentos decorativos.
”Este é o processo executivo de qualquer projeto de arquitetura.Não restringimos a criatividade do arquiteto e viabilizamos o projeto com maior rapidez, utilizando concreto de 25 a 30 MPa com slump entre 10 e 12”, comenta Sérgio Coelho.
CONSTRUÇÃO POPULAR COM QUALIDADE E RAPIDEZ
Visando oferecer ao mercado um sistema que viabilizasse a construção de edifícios voltado para o público de menor poder aquisitivo, sem que houvesse a perda de desempenho e qualidade , a InPar desenvolveu, depois de anos de estudos e visitas a diversos países, o “Projeto Viver” . O Projeto consiste em um sistema de construção baseado na utilização de paredes in loco, lajes planas nervuradas com fôrmas plásticas, esquadrias de PVC e instalações acessíveis em shafts e entre forros.
A parede é concretada em gabaritos, que , posteriormente, são substituídas por caixilhos, parafusados e colados com silicone estrutural.
Na avaliação do eng. Nelson Faversani Junior, gerente de obras da InPar, esse sistema permite uma significativa redução nos prazos para conclusão da obra,resultando em considerável economia no custo final do empreendimento.As paredes de concreto moldadas in loco também são bastante eficientes em termos de isolamento térmico e acústico, alem de eliminar problemas sérios de patologias de alvenaria.
A definição das características do concreto também foi fundamental para o “Projeto Viver”.”A princípio, achamos que seria necessário usar um concreto altamente plástico.Quando visitamos as obras que estavam sendo desenvolvidas na Itália e Israel, vimos que elas utilizavam concretos com slump 8. Após muitas pesquisas , chegamos ao traço que adotamos hoje, de slump 12 com pedra 1. Mas o fundamental para o nosso empreendimento é contar com concreto dosado em central de excelente qualidade”, explica o eng. Faversani. A especificação do fck é 20 MPa, com atenção especial para a composição dos agregados e a proporção entre areia e brita.
EDIFÍCIO DE 13 PAVIMENTOS EM 26 DIAS ÚTEIS
Já a construtora Sergus desenvolveu um sistema de que esta viabilizando a construção de edifícios,com alta qualidade e alta produtividade , cuja tecnologia consiste em paredes e lajes estruturais de concreto armado moldadas no local com o uso de fôrmas tipo túnel.Para os pavimentos-tipo a espessura mínima das paredes é de 12 cm e das lajes é de 8 cm.
Na avaliação do eng. Adalberto Magina, coordenador de qualidade da Sergus, esse sistema permite a racionalização da construção, em função de ciclos diários de montagem e desmontagem das fôrmas metálicas.”Com isso, conseguimos uma rapidez significativa na execução do edifício , pois produzimos dois apartamentos por ciclo de operação. Considerando-se quatro apartamentos por pavimento, as paredes e lajes são concluídas em aproximadamente 26 dias úteis para um edifício de 13 pavimentos”.
O objetivo de agilizar a construção mantendo-se a qualidade do empreendimento leva a uma natural preocupação com as características do concreto utilizado. “Para viabilizar este tipo de sistema construtivo, o concreto tem de ser de excelente qualidade, com alta resistência inicial, já que temos sempre que desenformar concretagem no dia seguinte”, analisa Adalberto. “Por este motivo, as próprias empresas prestadoras de serviços de concretagem fizeram parceria conosco,contribuindo para garantir a qualidade de nossos produtos”. O concreto empregado neste caso é de 25 MPa, com slump 18.
O sistema construtivo utilizado pela Sergus foi avaliado pelo IPT no que diz respeito as condições técnicas de produção, controle da qualidade e desempenho estrutural, acústico, térmico, estanqueidade à água, durabilidade e segurança ao fogo, tendo sido considerado adequado às condições de uso, conforme Referencia Técnica RT IPT n°11, de junho de 2000.
Créditos: Jornal Tecnologia do concreto armado N. 13
Nenhum comentário:
Postar um comentário